Tính đến nay đã có 358 doanh nghiệp sản xuất liên quan đến ngành công nghiệp ô tô gồm cả doanh nghiệp FDI và doanh nghiệp nội địa, trong đó có 50 doanh nghiệp lắp ráp ô tô, 45 doanh nghiệp sản xuất khung gầm, thân xe và thùng xe, 214 doanh nghiệp sản xuất linh kiện phụ tùng ô tô.
Số liệu trên được Cục Công nghiệp (Bộ Công thương) đưa ra tại hội thảo “Phát triển công nghiệp hỗ trợ ngành ô tô: Tác động chính sách, các rào cản và giải pháp” do Viện nghiên cứu quản lý kinh tế Trung ương (CIEM) tổ chức sáng nay 30/10.
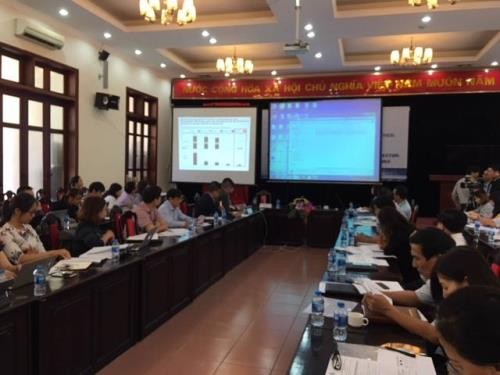
Toàn cảnh hội thảo
Mặc dù được đánh giá là gia tăng đáng kể về số doanh nghiệp trong thời gian gần đây, song con số này vẫn thấp hơn rất nhiều so với 385 doanh nghiệp ở Malaysia và 2.500 doanh nghiệp ở Thái Lan về sản xuất linh kiện phụ tùng ô tô.
Đến nay công nghiệp hỗ trợ ngành sản xuất, lắp ráp ô tô ở Việt Nam mới chỉ sản xuất được một số nhóm linh kiện, phụ tùng như chi tiết cấu thành khung gầm xe, thùng xe, vỏ cabin, cửa xe, săm lốp, bộ tản nhiệt, dây phanh, dây dẫn điện, trục dẫn, vành bánh xe, nhíp lò xo, ống xả, ruột két nước, hộp số, vô lăng…
“Đầu tư cho sản xuất linh kiện, phụ tùng ô tô còn mang tính nhỏ lẻ, sản phẩm làm ra ít cả về chủng loại và sản lượng. Sức cạnh tranh quốc tế của ngành sản xuất, lắp ráp ô tô còn hạn chế, nhất là sản phẩm của doanh nghiệp nội địa”, ông Lương Đức Toàn, Phó trưởng phòng Phòng Công nghiệp chế biến, chế tạo, Cục Công Nghiệp ( Bộ Công Thương) cho biết.
Theo ông Toàn, đối với các chủng loại xe tải, xe khách từ 10 chỗ ngồi trở lên, xe chuyên dụng sản xuất trong nước đã đạt tỷ lệ nội địa hoá cao, đáp ứng về cơ bản.
Cụ thể, xe tải 7 tấn đã đáp ứng khoảng 70% nhu cầu với tỷ lệ nội địa hoá trung bình 55%; xe khách từ 10 chỗ ngồi trở lên, một số loại xe chuyên dụng đáp ứng khoảng 90% nhu cầu tỷ lệ nội địa hoá đạt từ 45-55%.
Tỷ lệ nội địa hoá đối với xe cá nhân đến 9 chỗ ngồi đạt thấp, đến nay mới đạt bình quân khoảng 7-10%, trong đó Thaco đạt 15-18%, Toyota Việt Nam đạt 37% đối với riêng dòng xe Innova, thấp hơn mục tiêu đề ra.
Một số phụ tùng linh kiện đã xuất khẩu sang thị trường Lào, Campuchia, Myanmar, Trung Mỹ.
Tuy nhiên, phần lớn phụ tùng và linh kiện đều phải nhập khẩu. Năm 2014 nhập khẩu 2,2 tỷ USD; năm 2015 nhập khẩu 3 tỷ USD, năm 2016 nhập khẩu 3,5 tỷ USD và năm 2017 nhập khẩu 3,167 tỷ USD.
Trong khi đó, tỷ lệ mua phụ tùng trong nước tuỳ theo chủng loại xe và nhà sản xuất đạt 10-30% đối với xe du lịch; hơn 30% đối với xe tải và hơn 40% đối với xe buýt.
Phụ tùng, linh kiện chủ yếu được sản xuất và nhập khẩu từ doanh nghiệp FDI, tỷ lệ đặt hàng phụ tùng linh kiện từ doanh nghiệp nội địa cung cấp rất thấp. Trong số các doanh nghiệp cung cấp hiện có hơn 90% là doanh nghiệp FDI, chỉ có số ít doanh nghiệp trong nước có thể tham gia vào mạng lưới của doanh nghiệp cung cấp cho các doanh nghiệp sản xuất lắp ráp ô tô ở Việt Nam.
Ông Shinjiro Kajikawa, Phó giám đốc Toyota Việt Nam cho biết, thị trường biến động thường xuyên và sản lượng thấp dẫn đến việc nội địa hoá và hệ thống nhà cung cấp ở Việt Nam còn rất hạn chế, có tới 90% là nhập khẩu. Theo đó, cạnh tranh về chi phí sản xuất còn rất thấp.
Do sản lượng nhỏ và tỷ lệ nội địa hoá thấp nên chi phí sản xuất xe ở Việt Nam đang cao hơn xe nhập khẩu nguyên chiếc từ các nước ASEAN khoảng từ 10-20%.
Để mở rộng nội địa hoá, chúng tôi mong muốn Chính phủ sẽ cân nhắc các chính sách có hiệu quả để giảm chi phí đầu tư như hỗ trợ cho việc đầu tư khuôn ép và đồ gá…
- Ông Shinjiro Kajikawa, Phó giám đốc Toyota Việt Nam
Theo ông Shinjiro Kajikawa, sự phát triển của ngành công nghiệp ô tô không thể đạt được nếu thiếu sự tăng trưởng của thị trường, sản xuất lắp ráp xe trong nước và công nghiệp hỗ trợ.
Để ủng hộ cho công nghiệp hỗ trợ, linh kiện nội địa cần tăng khả năng cạnh tranh hơn so với linh kiện nhập khẩu về chất lượng, chi phí và giao hàng. Trong đó, chi phí, sản lượng đóng vai trò quan trọng.
“Việt Nam đang phải đối mặt với “sản lượng bất lợi” so với các nước khác. Vì vậy, để mở rộng nội địa hoá, chúng tôi mong muốn Chính phủ sẽ cân nhắc các chính sách có hiệu quả để giảm chi phí đầu tư như hỗ trợ cho việc đầu tư khuôn ép và đồ gá…” ông Shinjiro Kajikawa chia sẻ.
Để phát triển công nghiệp hỗ trợ ngành ô tô, đại diện Bộ Công thương khuyến nghị cần phải nâng cao năng lực doanh nghiệp công nghiệp hỗ trợ ngành ô tô đáp ứng yêu cầu của các chuỗi sản xuất toàn cầu thông qua việc triển khai hiệu quả Chương trình phát triển công nghiệp hỗ trợ.
Bên cạnh đó, thúc đẩy liên kết giữa các doanh nghiệp công nghiệp hỗ trợ và các doanh nghiệp sản xuất sản phẩm hoàn chỉnh bao gồm thị trường trong nước và ngoài nước đặc biệt với một số quốc gia như Nhật Bản, Hàn Quốc…
Đồng thời, hỗ trợ các doanh nghiệp nâng cao trình độ kỹ thuật và quản lý sản xuất, chuyển giao công nghệ, phát triển khoa học và công nghệ và phát triển nguồn nhân lực công nghiệp hỗ trợ.
Đặc biệt, trong đó hình thành gói tín dụng ưu đãi với cơ chế tương tự như gói tín dụng phát triển nông nghiệp công nghệ cao để phát triển các ngành công nghiệp ưu tiên. Hình thành các trung tâm hỗ trợ phát triển công nghiệp, phát triển các ngành công nghiệp hạ nguồn và thu hút đầu tư sản xuất sản phẩm công nghiệp hỗ trợ, trong đó là thu hút đầu tư FDI từ các tập đoàn sản xuất linh kiện hàng đầu thế giới.
Theo bà Nguyễn Thị Tuệ Anh, Phó Viện trưởng CIEM trước những cơ hội, thách thức khi hội nhập khu vực hoàn toàn, để có thể cạnh tranh được với các nước trong khu vực, Việt Nam cần có những giải pháp để thúc đẩy phát triển công nghiệp hỗ trợ ngành ô tô.
“Trong bối cảnh này rất cần tới các nghiên cứu chính sách liên quan đến ngành công nghiệp ô tô, công nghiệp hỗ trợ ngành ô tô; thực trạng và các giải pháp thúc đẩy phát triển công nghiệp hỗ trợ ngành ô tô là hết sức cần thiết”, bà Tuệ Anh nhấn mạnh.